21 February 2024
In-line chemical paint stripping of hooks and frames within the coating process
More and more coaters are choosing to paint strip the hooks and frames employed in their coating operations to avoid using them as disposable items. The standard method requires stopping production so they can be removed, replaced with new ones, and paint stripped separately. Aware of the importance of working with a continuous flow, however, ALIT Technologies has designed a plant that fulfills this task without interrupting the manufacturing cycle. FASTRIP ISP was conceived precisely to tackle the challenge of integrating the hook and frame paint stripping phase into coating lines.
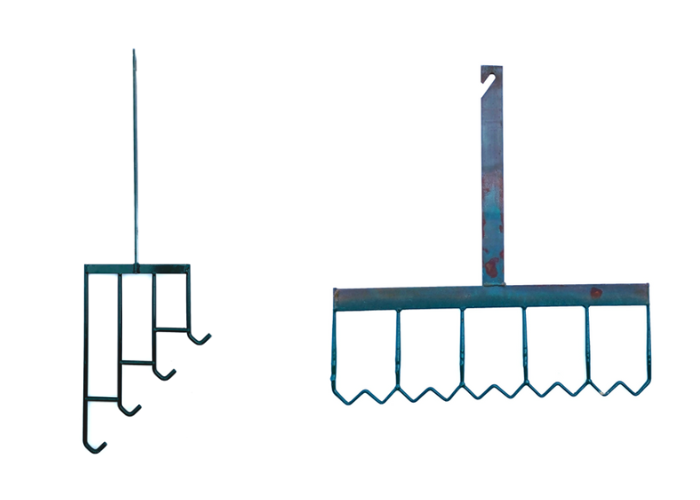
1. Hanging frames used for industrial coating operations
As mentioned, many companies today need to remove the paint residues deposited on their coating tools, including hanging hooks, load bars and frames, through a paint stripping operation aimed at re-using them.
But why do hooks and frames need to be cleaned?
Especially when it comes to electrostatic coating, the excellent electrical conductivity of the parts is of the essence. However, this can be significantly undermined by any impurities and paint layers deposited on the hooks and frames and acting as electrical insulators. Decreased conductivity also increases overspray, thus likely affecting the coating results. Therefore, paint stripping hooks and frames allows companies to re-use these accessories countless times without incurring the cost of buying new ones while ensuring flawless finishes.
FASTRIP ISP is ALIT Technologies’ solution for perfect in-line paint stripping of hooks and frames
Recognizing the importance of this process, ALIT Technologies accepted the challenge of developing an efficient solution for paint stripping hooks and frames. With this goal in mind, it designed and built FASTRIP ISP. Thanks to its modular design, this in-line chemical paint stripping system for hooks and frames can be easily integrated into existing production lines, ensuring the continuity of the coating cycle.
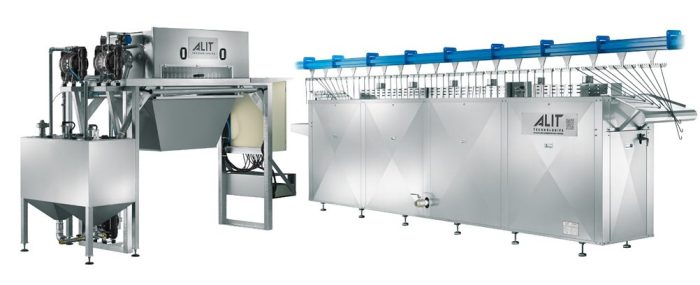
2. An example of a customized FASTRIP ISP machine for in-line paint stripping of hooks with a connected filter press
How is FASTRIP ISP made, and how does it work?
The FASTRIP ISP paint stripping system consists of two main units: the paint stripping tank and the FASTRIP FP series filtration system.
The tank is made of AISI 304 steel and contains an adjustable volume of paint stripper, which is simultaneously heated and subjected to ultrasonic waves. The combined effect of the chemical attack by the paint stripper, high temperature, and ultrasound allows removing a paint layer in as little as 3 minutes. While remaining hooked onto the overhead conveyor, the items to be paint-stripped are partially submerged into the stripping tank as they pass through. The tank’s linear length is proportional to the coating line’s speed, usually within a range of 4-8 meters. The paint stripping product is heated by electric heating plates attached externally to the tank, guaranteeing high standards of safety and ease of maintenance at the same time. The ultrasonic batteries are also externally flanged, easy to access, and highly robust. The tank is insulated to minimize heat loss and its shape optimizes sludge filtration.
The FASTRIP FP series filtration system is connected to the paint stripping tank and allows consistent removal of the coating sludge that accumulates in the bath. Sludge is continuously removed from the tank’s bottom and filtered with a filter press. The clean paint stripper can then be automatically recirculated to the paint stripping tank. The configuration options of the filter press, liquid tanks and piping are extremely varied and can be customized according to customer needs.
Adding a water rinse module to remove any paint stripping oil residues and an infrared lamp system for drying is also possible.
What are the advantages of this plant?
The benefits of using FASTRIP ISP for paint stripping hooks and frames are numerous:
- the system enables to perform paint stripping operations without removing the hooks from the chain;
- the process is easier to manage, as there is no need for downtime to clean the tank;
- the labor involved in managing the hooks (i.e. cyclically removing the dirty ones and positioning the clean ones) is significantly reduced;
- hooks and frames are always clean;
- thanks to its modular design, the system can reach any length, as well as a hook and frame immersion depth of up to 30 cm.
- FASTRIP ISP can be used for paint stripping any metal because it is not aggressive to surfaces, even with light alloys. Hooks and frames will always be as good as new!
The ideal chemicals for FASTRIP ISP
One of the goals of ALIT Technologies is to offer complete systems that provide all-round solutions. The market demanded a plant capable of paint stripping the hooks and frames used in coating processes – and the ALIT team met this need by designing and launching FASTRIP ISP. Of course, this type of plant also requires the use of chemical agents, so ALIT Technologies also developed a wide range of paint stripping products that guarantee optimal results when combined with the FASTRIP ISP system. These include as follows:
- 14XX Series METALSTRIP
These paint strippers are used to fill the tank during the plant’s start-up. Usually, their use is limited to this phase.
- 16XX Series METALSTRIP AKTIVATOR
They are used routinely to feed the paint stripping tank during regular operation. They should be added periodically to maintain optimal bath chemical parameters. The operator determines the quantities to be added through a simple chemical analysis of the bath.
- COVER LAYER Series METALSTRIP
This non-toxic liquid forms a floating layer of about 4 cm above the paint stripper in the tank. It helps reduce heat loss and odor emissions and preserve the paint stripper from contact with air.
- METALSTRIP 1465
This new product has improved fluidity and sludge settling capacity characteristics. One of its main features is its full compatibility with ALIT Technologies’ other paint stripper series, meaning that it can be added directly into the FASTRIP ISP tank, gradually replacing the product used previously without the need to refill the tank completely.
All these products are part of ALIT’s METALSTRIP product range, and in addition to providing excellent performance, they meet strict environmental sustainability requirements.
A case study testifying to the effectiveness of FASTRIP ISP
Background
A major company in Northern Italy producing and marketing wire mesh, fences and gates asked us to supply two complete FASTRIP ISP plants for paint stripping its hooks and frames. The paints to be removed were polyester coatings and the size of the hooks ranged from 70 cm in height to 50 cm in width.
The issue
The company had two already existing coating lines: due to space constraints and the chain’s layout, we had to design two custom plants with elevated paint stripping tanks.
Our solution
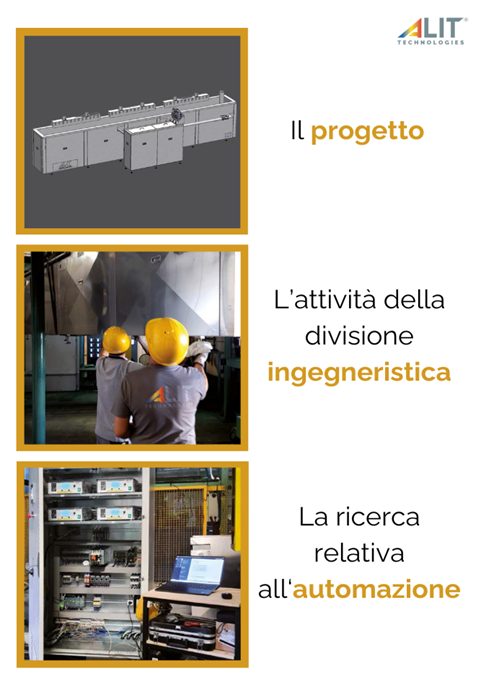
ALIT’s Engineering division conducted a detailed geometric survey of the space available and the overhead conveyor in the area of interest. It then presented the customer with a design that was gradually refined until approval. The paint stripping and filtration areas were designed to fit into the existing spaces without interfering with the adjacent coating and robotic unloading areas.
With regard to automation, it was agreed that the plant would comply with INDUSTRY 4.0 standards. The main switchboard was equipped with advanced technologies to exchange process data with the customer’s management software and allow for remote service and monitoring. The wiring and insulation materials on board the machine were selected based on ALIT’s experience in the paint stripping industry, balancing the required chemical and thermal resistance characteristics.
The company protagonist of this case study has undoubtedly obtained many benefits from its new FASTRIP ISP. In addition to radically decreased costs, opting for this plant from ALIT Technologies has enabled it to lower its environmental impact, reduce its long-term costs and increase its turnover by eliminating the need to stop the coating line.
Would you also like to implement such an innovative system for your business?
Get in touch with the ALIT team: together, we will identify the most suitable solution for your production needs!