10 June 2024
Revolution in extrusion dies cleaning: how Claris 9346MB transformed die cleaning for Extrusal S.A.
At the heart of the dynamic Portuguese company Extrusal S.A., a big change is revolutionising the extrusion die cleaning process. Through the introduction of Claris 9346MB, an innovative product, Extrusal has achieved relevant results that are changing the landscape of the dies cleaning plant managing. Let’s find out how this winning partnership has not only optimised Extrusal’s operational efficiency but also contributed to a more sustainable management of the environment.
Before we dive into the wonderful technicalities of Claris and its effects, it is only right to introduce you to Extrusal, who it is and what it does!
EXTRUSAL S.A. is a Portuguese company operating in the metallurgical sector, specializing in the extrusion of aluminium components and profiles for the construction industry (window and door systems, shading and cladding solutions, railings, and facade systems), general industry (transportation, engineering, energy, among others), and the automotive industry. Founded in March 1972, Extrusal has consistently remained at the forefront of technology, with a primary focus on the quality of its products and services to ensure maximum satisfaction for both direct and indirect clients.
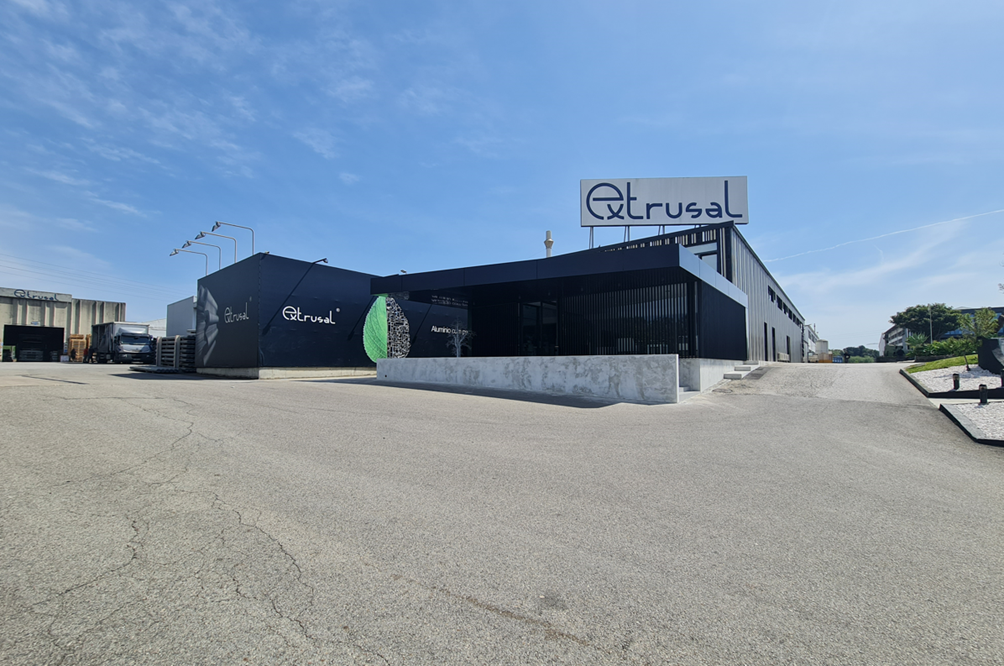
Extrusal S.A. headquarters in Aveiro, Portugal.
Currently, the industry represents approximately 74% of the company’s turnover (26% automotive industry and 43% general industry), with direct exports accounting for 37%. Architectural sector exports primarily target PALOP countries, while the Industry sector exports to Europe.
Extrusal’s production process consists of:
- Engineering and Development Department: Equipped with the latest CAD/CAM systems, it plays a crucial role in internal R&D. Collaborating with the Product Marketing Department and the Prototyping Center, this department develops technical solutions for the Construction sector;
- Die Factory: Extrusal has an autonomous die factory that produces the majority of the dies used in the extrusion process. It is equipped with milling machines, machining centers, non-conventional lathes, turning CNC machines and EDM. The increasing complexity of products makes die manufacturing an increasingly important step in Extrusal’s production process;
- Extrusion: Extrusal currently operates two extrusion lines (17MN and 20MN) with an annual extrusion capacity of approximately 13,000 tons (depending on productivity and profile type). The company has a dedicated Extrusion support laboratory for R&D of extrusion profiles and their control, conducting tests such as tensile tests, Brinell hardness, Webster hardness measurement, and roughness tests;
- Machining: The machining section is equipped with saws, presses, milling machines, balancers, bending machines, and various dedicated equipment. Extrusal’s machining process complies with the NP EN ISO 9001 standard;
- Thermal Cutting: Extrusal was the first company in Portugal to produce thermal cutting systems for architecture, with a dedicated production line;
- Surface Treatments (powder coating, anodizing, and wood effect decoration): Extrusal has three sections dedicated to each type of in-house surface treatment. For anodizing, an electrolytic process, Extrusal has held Qualanod certification (no. 1405) since 1983. Powder coating, a Thermosetting coating process, has also been certified by Qualicoat since 1995. An internal laboratory ensures the quality control of processes and products.
Extrusal was the first Portuguese company, and one of the few in Europe, to obtain certification for the global quality management system – NP EN ISO 9002 – in the areas of die manufacturing, extrusion, anodizing, and .Thermosetting powder coating. Additionally, in 1997, Extrusal was the first Portuguese company, and one of the few in Europe, to obtain certification for the global quality management system – NP EN ISO 9002 – in the areas of die manufacturing, extrusion, anodizing, and powder coating.
A pioneer in environmental defense and preservation, Extrusal built a wastewater treatment plant in 1982. Environmental awareness has driven the acquisition of new equipment and technologies, leading to the implementation of an Environmental Management System and obtaining ISO 14001 environmental certification in 2002. Process optimization and a focus on reuse/recycling have been fundamental at Extrusal. The company has embraced an ecological organizational culture with all stakeholders, promoting sustainable practices throughout the organization.
In the architectural sector, the focus is on developing solutions using recyclable or recycled materials, energy-efficient, and durable. Extrusal’s portfolio includes hinged and sliding systems, cladding systems, shading solutions, facade systems, balustrading solution, shutters, and aluminium systems for indoor use. Window and door solutions undergo tests for thermal, acoustic, and AEV (air permeability, water tightness, and wind resistance) performance. Extrusal is one of the pioneering companies in adopting the Class+ labeling system promoted by ADENE.
Extrusal offers a wide range of solutions for the Industry sector, leveraging aluminium’s characteristics such as lightness, conductivity, durability, malleability, recyclability, and non-toxicity across various industries (from food to aerospace). For the automotive sector, Extrusal develops structural and decorative components with high-quality finishing. The company also contributes to the solar industry through its “Pro-Solar” solutions, designing and developing innovative aluminium structures for mounting solar panels or collectors.
Last but not least, alongside offering pre-conceived profiles, Extrusal provides clients with the opportunity to present their own projects.
Now that we have laid the groundwork for the case history of Extrusal S.A., it is time to dive into the practical part that will capture the attention of the industry’s technicians. We will explore how the use of the Claris 9346MB in the mould cleaning department has brought observable benefits and revolutionised the way Extrusal approaches this crucial operational aspect.
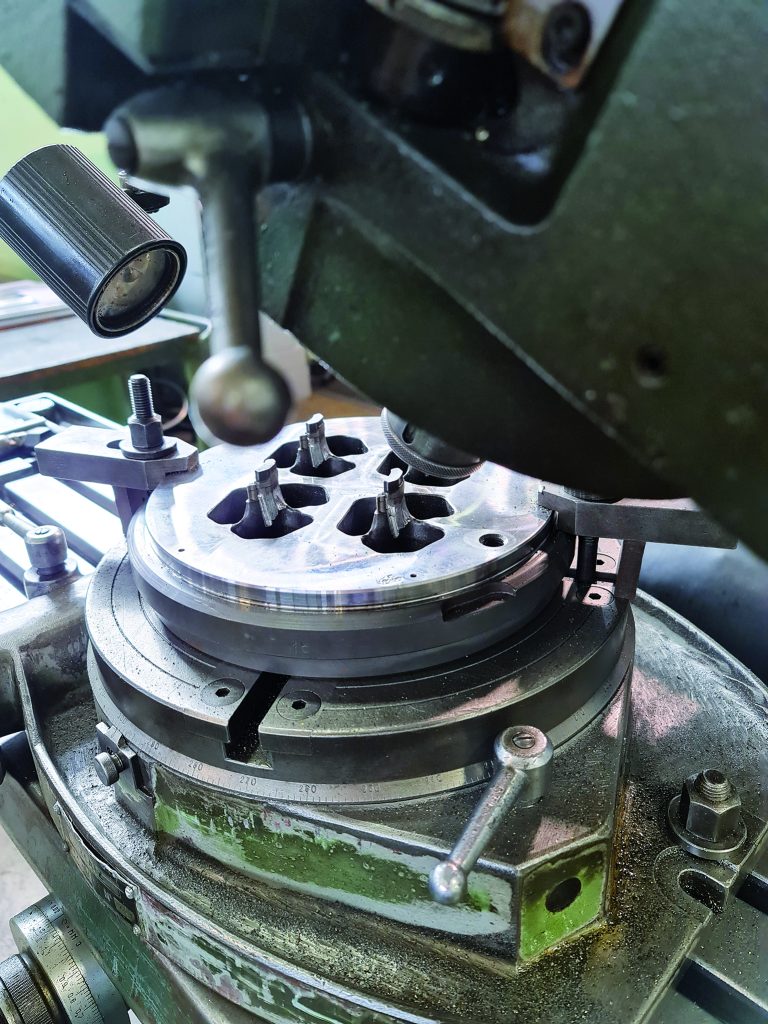
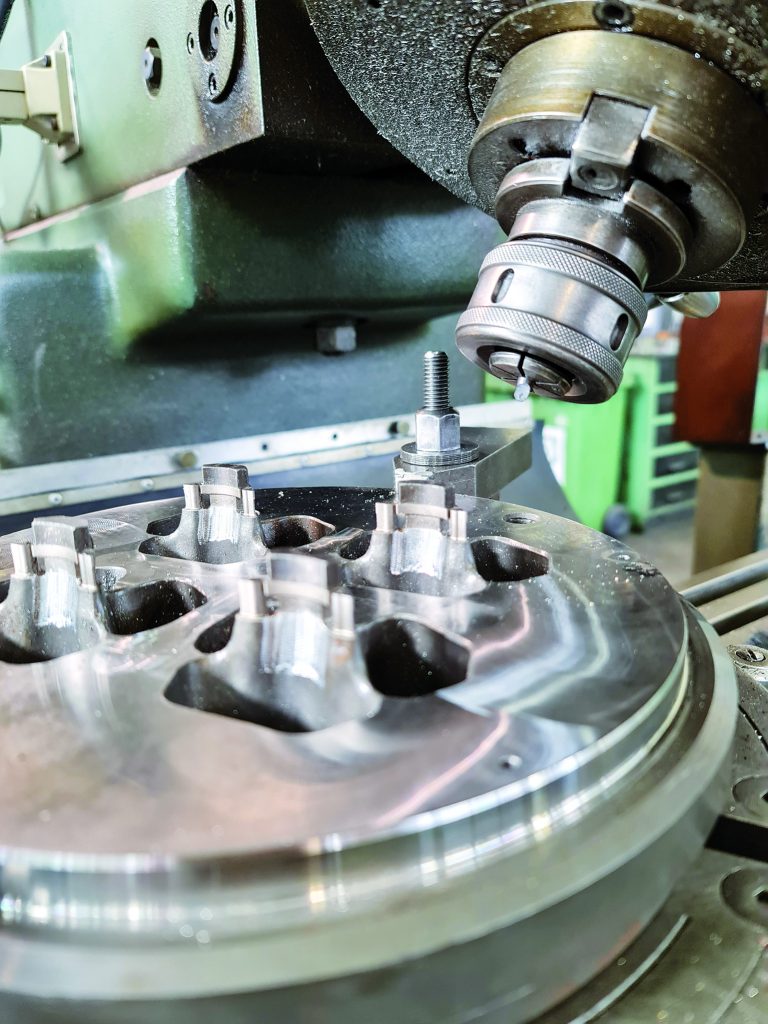
Dimensional Quality control of dies by Extrusal S.A.
The die cleaning tank used in Extrusal has a nominal volume of 1000 litre. Before the introduction of CLARIS in this plant the customer was using the dye cleaning solution, consisting in sodium hydroxide 30% w/w, for 24hours. As described by our colleague Pedro Oliveira “After this time has elapsed the alkaline solution was regularly dismissed because it was exhaust, no longer useful for cleaning of new extrusion dies. Practically there was a consumption of about 1000 litre of NaOH 30% every 24h work, and during this time the average amount of cleaned materials was about 6 baskets of extrusion dies”. Pedro continues by telling us that “After a visit to the die cleaning plant, and after collection of the preliminary technical date, it was organized a first test with Claris 9346MB. It was prepared the 1000 litre of NaOH 30% as usual, and it was added 25 g/l of CLARIS 9346MB, namely 25 Kg. Then the operators started the cleaning of extrusion dies as usual. After 24 hours, the operators realized that the bath was still effective, i.e still able to clean the extrusion dies, so a new cleaning cycle was started without changing the alkaline solution and without adding again CLARIS 9346MB. The cleaning of materials in this second cycle of 24h was perfectly efficient and after a total of 48 hours of use, the die cleaning bath was disposed of”. Pedro tells us that “with great customer satisfaction, the lifetime of the alkaline solution was doubled, without compromising its efficiency and productivity in any way“. The thermographic profiles collected against time are shown in Fig 1.
Pedro explains to us that “The blue colour profile refers to the test conducted WITHOUT Claris 9346MB, while the orange colour profile refers to the test conducted WITH 25g/l of Claris 9346MB dissolved in the alkaline cleaning solution. It can be observed that in the presence of CLARIS 9346MB, after about 24 hours, it was possible to insert a new load of baskets into the die cleaning tank, the temperature of the bath rose (also thanks to the exothermic reaction of aluminium dissolution) up to around 90°C, and then gradually dropped to at approximately 80°C over the next 24 hours. The thermographic profile was similar to that of the solution (blue line) without CLARIS, but the lifetime of the alkaline solution was double: An addition of 25 Kg of CLARIS 9346MB permit to the cleaning solution to treat double quantity of parts: truly fantastic!”
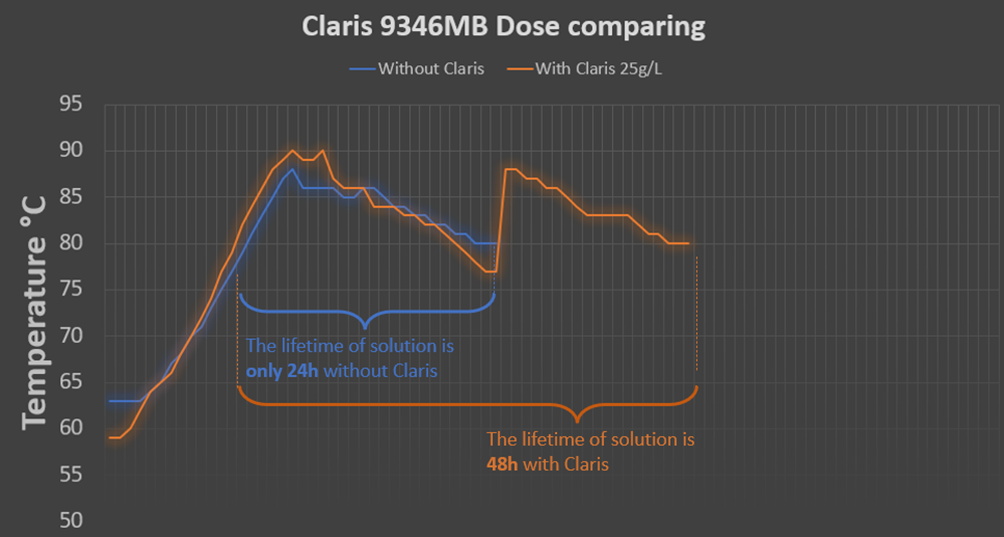
Fig 1: Thermographic profile of the alkaline cleaning solution without (blue) and with CLARIS 9346MB
We asked Pedro to explain us why the presence of Claris prolongs so much the lifetime of the extrusion die cleaning bath. And he replied that ” Cleaning an extrusion die means first removing the solidified aluminium that remains in the holes of the die. If Claris 9346MB is present in the alkaline solution, the dissolution process of the solid aluminium is modified, and thanks to Claris 9346MB it becomes in practice possible to mechanically extract the aluminium block from the matrix without dissolving too much of it in the liquid solution. In this way the process bath is not enriched too much with aluminium, and therefore remains much more active. To the point that, in the presence of a correct dosage of Claris 9346MB, the quantity of treatable dies can be doubled”.
An example of aluminium residues that can be extracted from extrusion dies without dissolving too much aluminium in the alkaline solution is visible in Fig. 2.
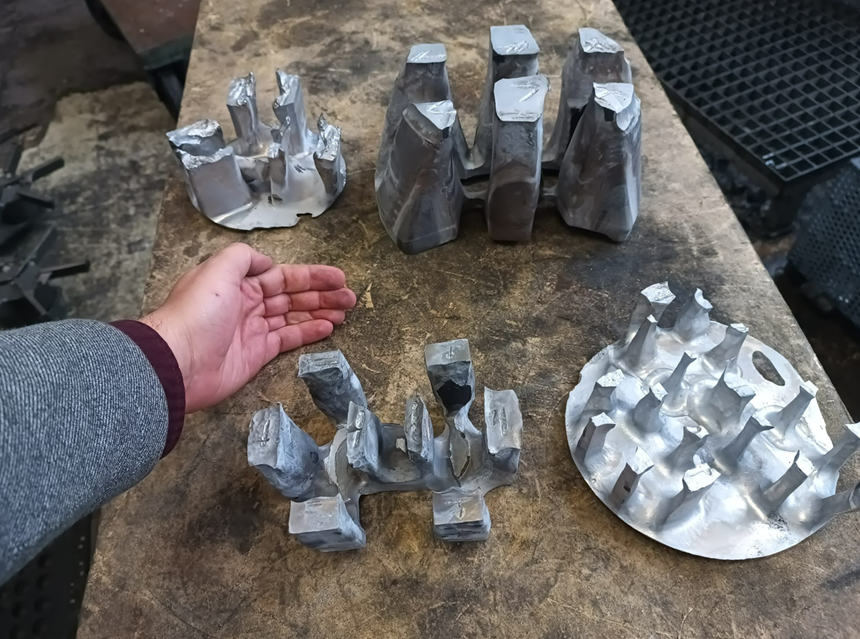
Fig 2: residual aluminium blocks extracted from extrusion dies using 25g/l of CLARIS 9346MB in the alkaline solution.
Without CLARIS 9346MB | With CLARIS 9346MB | |
Lifetime of alkaline solution | 24h | 48h |
Al (TOTAL) dissolved in the exhaust cleaning solution | 105 g/l | 105 g/l |
n° of treated die basket | 6 | 12 |
Pedro confirms that “The use of Claris 9346MB at Extrusal S.A. it is now a consolidated practice, and the customer declares himself fully satisfied with the benefits deriving from its introduction in the dies cleaning process. The consumption of alkaline solution has been significantly reduced and with it the disposal of used alkaline solutions. From the environmental point of view, much more aluminium can be recycled and thanks to the controlled reaction, less gas is expelled into the atmosphere. This die cleaning process reduces smells in the working area, ensuring better working conditions to the operators”.
CONCLUSION:
Claris 9346MB is an innovative additive for aluminum extrusion die cleaning, offering enhanced efficiency, cost savings, and extended bath life. It significantly improves the cleaning process, ensuring better performance and sustainability. Want to learn more? Visit our product page and contact us through our form. Follow ALIT Technologies on LinkedIn to stay updated with the latest advancements. Our commercial and technical staff are ready to assist you with any inquiries!